A brief analysis of the important basis of chemical valve selection
- Share
- Issue Time
- May 25,2020
Summary
Valve in petroleum, chemical equipment is an important component, any process of successful operation is inseparable from the correct selection of the valve.
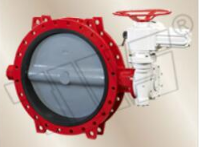
Valve in petroleum, chemical equipment is an important component, any process of successful operation is inseparable from the correct selection of the valve.
The rational selection of valves includes professional design work of chemical process, process system, chemical safety and environmental protection, energy conservation, pipeline and equipment layout, and takes into account the fluid nature, operating conditions, external environment, economy and the requirements of relevant laws, regulations and standards.
1. From the perspective of fluid properties, the following aspects should be considered comprehensively: chemical, molecular formula, impurity and content of the fluid;Hazards of the fluid (such as toxicity, flammability, and corrosiveness);Physical properties of the fluid (such as density, viscosity, rheological properties);Chemical properties of the fluid (reactivity, thermal effect, reaction rate, polymerization, scaling, oxidation, PH value, etc.).
2. In terms of operating conditions, in addition to the design conditions of normal operation, the large and small values, operating modes of various operating conditions and the large change rate of operation are considered in all operating conditions (including fault conditions).
Because the valve's pressure temperature rating is based on stable operating conditions, that is, assuming that the process operating conditions change slowly enough, the valve is designed for all parts without pressure pulsation or thermal shock.Pressure pulsation, vibration and thermal shock can cause serious valve problems.Mild effects of thermal shock are biting and sticking, severe thermal shock can cause body cracking and seal damage.
Pressure pulsation and vibration can lead to rapid wear and tear of valve moving parts, and pressure cycle pulsation can lead to material fatigue failure.When selecting valve, the factors of pressure pulsation, vibration and thermal shock should be considered.
3, from the flow conditions, the normal operation of the valve, valve flow in the turbulent area.High speed flow regulating or throttling valves, the flow through the tortuous passage of high turbulence, may cause vibration or noise (gas).
When selecting valve type and size, pay attention.Safety relief valve, blocking flow of two-phase flow, rapid closing of valve or closing of check valve when pump failure stops, etc., will cause rapid change of pressure and flow, resulting in (air) water hammer phenomenon.(gas) water hammer phenomenon produces noise, vibration, resulting in valve damage.In order to prevent water hammer, the operating mechanism (handwheel, handle) or the device with uniform switch of the driving device should be set, or the anti-impact facilities (such as slow closing tank, gas-liquid separation tank, etc.) should be set on the pipeline.At the same time, the two - phase flow has a great influence on the correct selection of valves.
Flash and gas erosion occur when the pressure drop of liquid through the valve is too large and the pressure at the throttle outlet is equal to or below the saturated vapor pressure of liquid.This will not only reduce the flow capacity and sealing performance of the valve, but also seriously damage the body, seat, spool and sealing structure, and even cause valve pressure problems.Therefore, cavitation resistant valve types, cavitation resistant valve cores and surface-hardened alloy materials with rockwell hardness exceeding HRC40 are selected.High - speed gas (vapor) flow with droplet also causes cavitation.Entrainment of solid particles in the flow of gas (vapor) or liquid flow has greater erosion, wear action.